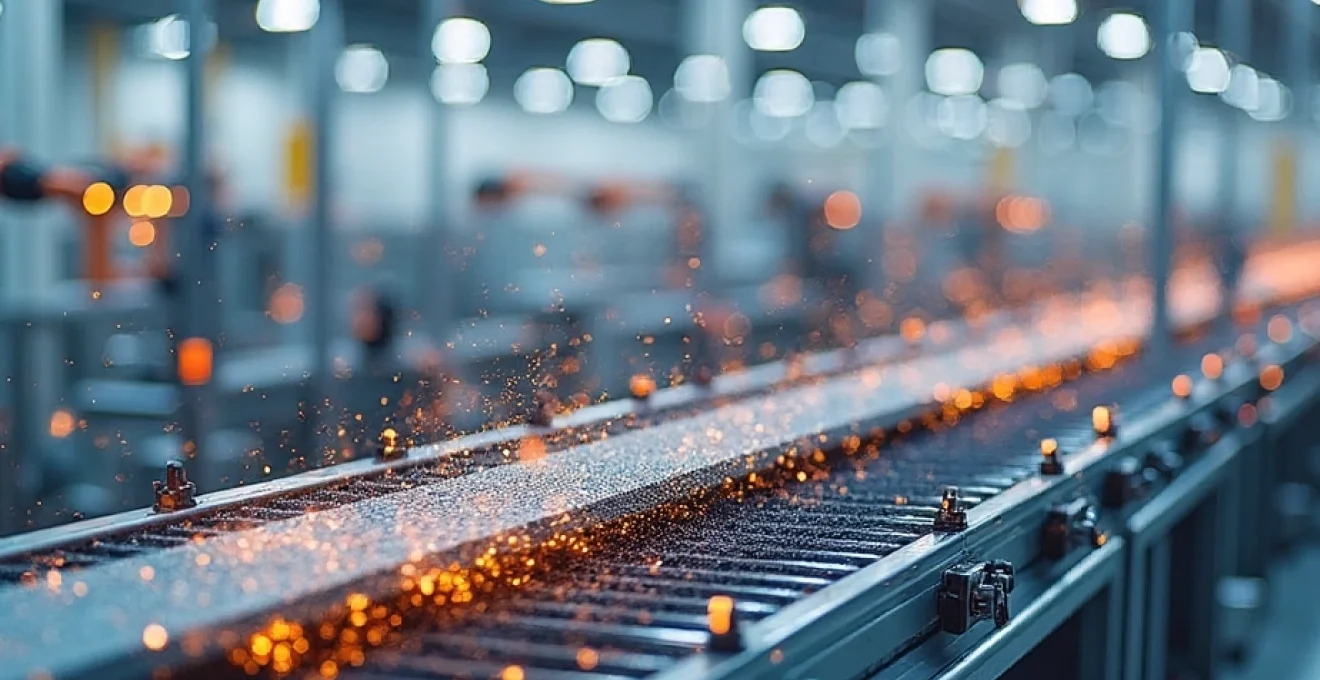
L’automatisation des chaînes de production représente un enjeu majeur pour les industries cherchant à gagner en efficacité et en compétitivité. Une conception optimale permet non seulement d’accroître la productivité, mais aussi d’améliorer la qualité des produits tout en réduisant les coûts opérationnels. Cette démarche complexe nécessite une approche systémique et l’intégration de technologies de pointe pour créer des systèmes flexibles, intelligents et évolutifs.
Analyse systémique des processus de production automatisés
L’optimisation d’une chaîne de production automatisée débute par une analyse approfondie des processus existants. Cette étape cruciale permet d’identifier les goulots d’étranglement, les inefficacités et les opportunités d’amélioration. Elle implique l’étude détaillée des flux de matériaux, d’informations et d’énergie au sein du système de production.
Une approche systémique prend en compte les interactions entre les différents composants de la chaîne, plutôt que de les considérer isolément. Cela permet de comprendre comment une modification à un niveau peut impacter l’ensemble du système. Par exemple, l’introduction d’un nouveau robot d’assemblage peut nécessiter des ajustements dans l’approvisionnement en pièces ou dans la programmation des tâches en aval.
L’analyse des données de production historiques joue un rôle central dans cette démarche. Elle permet d’identifier les tendances, les variations saisonnières et les corrélations entre différents paramètres. Ces informations sont précieuses pour dimensionner correctement les équipements et optimiser les flux de production.
Conception modulaire et flexibilité opérationnelle
Une chaîne de production moderne se doit d’être flexible pour s’adapter rapidement aux évolutions du marché et aux changements de gammes de produits. La conception modulaire répond à cet impératif en permettant de reconfigurer facilement les lignes de production. Cette approche repose sur l’utilisation de modules standardisés et interchangeables, facilitant les modifications et les mises à niveau du système.
La flexibilité opérationnelle se traduit également par la capacité à produire différentes variantes de produits sur une même ligne, avec des changements de série rapides. Cela nécessite des équipements polyvalents et des systèmes de contrôle adaptatifs capables de gérer une grande diversité de paramètres de production.
Intégration de robots collaboratifs kuka et universal robots
Les robots collaboratifs, ou cobots , représentent une avancée majeure dans l’automatisation flexible. Contrairement aux robots industriels traditionnels, ils peuvent travailler en toute sécurité aux côtés des opérateurs humains. Les cobots Kuka et Universal Robots se distinguent par leur facilité de programmation et leur capacité à être rapidement redéployés pour différentes tâches.
L’intégration de ces robots dans la chaîne de production permet d’automatiser des tâches complexes tout en conservant la flexibilité nécessaire pour s’adapter aux variations de production. Leur polyvalence les rend particulièrement adaptés aux environnements de production mixtes, où la collaboration homme-machine est essentielle.
Systèmes de convoyage interroll pour flux de matériaux optimisés
Les systèmes de convoyage jouent un rôle crucial dans l’optimisation des flux de matériaux au sein d’une chaîne de production automatisée. Les solutions Interroll se distinguent par leur modularité et leur efficacité énergétique. Elles permettent de créer des flux de matériaux fluides et adaptables, essentiels pour maintenir une production continue et éviter les accumulations.
Ces systèmes intègrent des technologies avancées comme le contrôle de zone, qui permet de gérer intelligemment l’accumulation et la séparation des produits sur le convoyeur. Cette fonctionnalité est particulièrement utile pour synchroniser les flux avec les différentes étapes de production et optimiser l’utilisation des ressources en aval.
Capteurs intelligents et IoT industriel pour le contrôle en temps réel
L’intégration de capteurs intelligents et de technologies IoT (Internet des Objets) industrielles permet un contrôle en temps réel de l’ensemble de la chaîne de production. Ces dispositifs collectent en continu des données sur les performances des équipements, la qualité des produits et les conditions environnementales.
L’analyse de ces données en temps réel permet d’identifier rapidement les anomalies et d’ajuster les paramètres de production pour maintenir une qualité optimale. Elle facilite également la mise en place de stratégies de maintenance prédictive, réduisant ainsi les temps d’arrêt imprévus.
Interfaces homme-machine ergonomiques avec écrans tactiles siemens
Les interfaces homme-machine (IHM) jouent un rôle clé dans l’efficacité opérationnelle d’une chaîne de production automatisée. Les écrans tactiles Siemens offrent des solutions ergonomiques permettant aux opérateurs de surveiller et de contrôler facilement les processus de production complexes.
Ces interfaces intuitives facilitent l’accès aux informations critiques et permettent des interventions rapides en cas de besoin. Elles contribuent ainsi à réduire les erreurs humaines et à améliorer la réactivité face aux aléas de production.
Optimisation des flux par simulation numérique
La simulation numérique est devenue un outil incontournable pour optimiser la conception et le fonctionnement des chaînes de production automatisées. Elle permet de tester virtuellement différentes configurations et scénarios de production avant leur mise en œuvre physique, réduisant ainsi les risques et les coûts associés aux modifications de la ligne.
Modélisation 3D avec logiciel tecnomatix plant simulation
Le logiciel Tecnomatix Plant Simulation de Siemens offre des capacités avancées de modélisation 3D des chaînes de production. Il permet de créer des modèles détaillés intégrant tous les éléments de la ligne, des machines aux opérateurs en passant par les systèmes de convoyage.
Cette modélisation précise permet d’analyser finement les interactions entre les différents composants de la chaîne et d’identifier les opportunités d’optimisation. Elle facilite également la communication entre les différentes parties prenantes du projet, grâce à une visualisation claire et intuitive du système.
Analyse des goulots d’étranglement et équilibrage des lignes
L’un des principaux avantages de la simulation numérique est sa capacité à identifier rapidement les goulots d’étranglement dans la chaîne de production. Ces points critiques limitent le débit global de la ligne et doivent être optimisés en priorité.
L’analyse des résultats de simulation permet d’équilibrer efficacement les charges de travail entre les différents postes, maximisant ainsi l’utilisation des ressources. Elle aide également à dimensionner correctement les zones tampons entre les étapes de production pour absorber les variations de cadence.
Scénarios de production et planification prédictive
La simulation permet de tester différents scénarios de production, prenant en compte des variations de demande, des pannes d’équipement ou des changements de gamme de produits. Cette approche prédictive aide à anticiper les problèmes potentiels et à développer des stratégies d’adaptation efficaces.
En intégrant des données historiques et des prévisions de marché, il devient possible d’optimiser la planification de la production à moyen et long terme. Cela contribue à améliorer la réactivité de l’entreprise face aux fluctuations de la demande et à optimiser l’utilisation des ressources.
Intégration de l’intelligence artificielle et du machine learning
L’intelligence artificielle (IA) et le machine learning ouvrent de nouvelles perspectives pour l’optimisation des chaînes de production automatisées. Ces technologies permettent d’analyser de vastes volumes de données pour identifier des patterns complexes et prendre des décisions autonomes en temps réel.
Dans le contexte de la production, l’IA peut être utilisée pour optimiser dynamiquement les paramètres de fabrication, prédire les pannes d’équipement, ou encore ajuster les plans de production en fonction des variations de la demande. Le machine learning, quant à lui, permet d’améliorer continuellement les performances du système en apprenant des données historiques et des résultats obtenus.
L’intégration de ces technologies nécessite une infrastructure de collecte et de traitement de données robuste, ainsi qu’une expertise en data science. Cependant, les bénéfices potentiels en termes d’efficacité et de flexibilité sont considérables.
L’IA et le machine learning transforment les chaînes de production en systèmes autonomes capables de s’auto-optimiser en continu.
Sécurité et conformité réglementaire des systèmes automatisés
La sécurité est un aspect fondamental dans la conception et l’exploitation des chaînes de production automatisées. Elle concerne à la fois la protection des opérateurs et la sécurité des processus eux-mêmes. La mise en place de systèmes de sécurité intégrés, conformes aux normes en vigueur, est essentielle pour prévenir les accidents et garantir la fiabilité de la production.
Les réglementations en matière de sécurité des machines et d’automatisation industrielle évoluent constamment. Il est crucial de se tenir informé des dernières normes et directives, telles que la directive Machines 2006/42/CE en Europe ou les standards ANSI/RIA aux États-Unis. La conception de la chaîne de production doit intégrer ces exigences dès les premières phases du projet.
Les systèmes de sécurité modernes s’appuient sur des technologies avancées comme les barrières immatérielles, les scanners laser de sécurité ou encore les systèmes de contrôle de mouvement sécurisés. Ces dispositifs permettent de créer des zones de travail collaboratives où hommes et robots peuvent coexister en toute sécurité.
Maintenance prédictive et gestion du cycle de vie
La maintenance prédictive représente un pilier essentiel de l’optimisation des chaînes de production automatisées. En anticipant les pannes et en planifiant les interventions de maintenance, elle permet de réduire considérablement les temps d’arrêt imprévus et d’optimiser la durée de vie des équipements.
Capteurs vibratoires SKF pour surveillance des équipements
Les capteurs vibratoires SKF sont des outils puissants pour la surveillance en continu de l’état des machines tournantes. Ils permettent de détecter précocement les signes de dégradation mécanique, tels que les défauts de roulements ou les désalignements.
L’analyse des données vibratoires fournit des informations précieuses sur l’état de santé des équipements, permettant de planifier les interventions de maintenance au moment le plus opportun. Cette approche contribue à maximiser la disponibilité des machines tout en réduisant les coûts de maintenance.
Analyse des données avec plateforme IBM watson IoT
La plateforme IBM Watson IoT offre des capacités avancées d’analyse des données collectées par les différents capteurs de la chaîne de production. Elle utilise des algorithmes d’intelligence artificielle pour identifier les tendances et prédire les défaillances potentielles.
Cette analyse prédictive permet d’optimiser les stratégies de maintenance en identifiant les composants susceptibles de tomber en panne et en recommandant des actions préventives. Elle contribue ainsi à améliorer la fiabilité globale du système de production.
Planification des interventions et gestion des pièces détachées
Une gestion efficace de la maintenance prédictive nécessite une planification rigoureuse des interventions et une optimisation des stocks de pièces détachées. Les systèmes de gestion de la maintenance assistée par ordinateur (GMAO) jouent un rôle clé dans ce processus.
Ces outils permettent de planifier les interventions en fonction des prédictions de défaillance, tout en tenant compte des contraintes de production. Ils aident également à optimiser la gestion des stocks de pièces détachées, en s’assurant que les composants critiques sont disponibles au bon moment.
Formation des opérateurs à la maintenance de niveau 1
La formation des opérateurs aux tâches de maintenance de premier niveau est un aspect souvent négligé mais crucial de l’optimisation des chaînes de production. En dotant les opérateurs des compétences nécessaires pour effectuer des interventions simples, on peut réduire significativement les temps d’arrêt et améliorer la réactivité face aux problèmes mineurs.
Cette approche, connue sous le nom de Total Productive Maintenance (TPM), implique une responsabilisation accrue des opérateurs dans le maintien en condition opérationnelle des équipements. Elle nécessite un programme de formation structuré et un suivi régulier pour s’assurer que les compétences sont maintenues à jour.
L’optimisation de la conception finale d’une chaîne de production automatisée est un processus complexe qui nécessite une approche holistique. Elle implique l’intégration de technologies avancées, une analyse approfondie des processus, et une attention particulière à la flexibilité et à la maintenance. En adoptant ces principes et en restant à l’écoute des innovations du secteur, les industriels peuvent créer des systèmes de production hautement performants, capables de s’adapter aux défis futurs du marché.