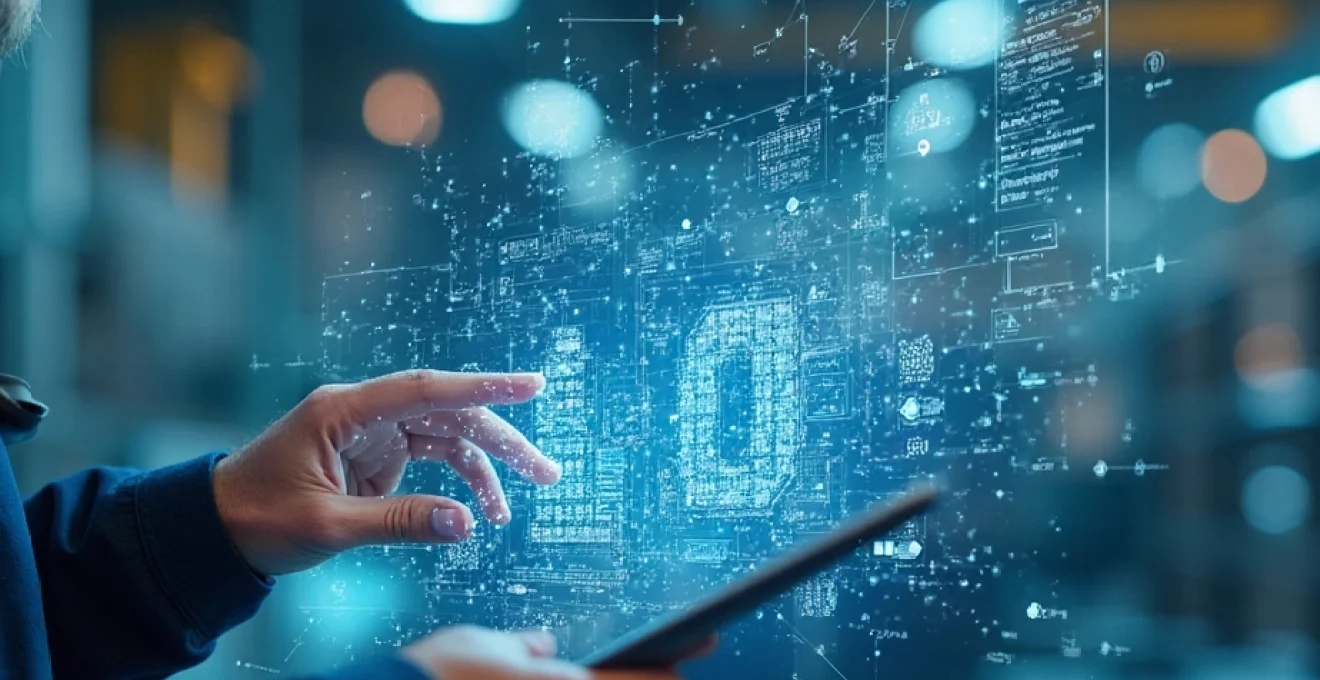
L’industrie 4.0 représente une transformation profonde du secteur manufacturier, propulsée par des avancées technologiques révolutionnaires. Cette nouvelle ère industrielle se caractérise par l’intégration de systèmes cyber-physiques sophistiqués, l’exploitation massive de données et une connectivité sans précédent entre les machines, les processus et les humains. Les usines intelligentes qui en résultent sont capables d’une flexibilité et d’une efficacité inédites, redéfinissant les paradigmes de production traditionnels.
L’impact de ces innovations technologiques sur la fabrication est considérable. Des capteurs intelligents aux algorithmes d’apprentissage automatique, en passant par la réalité augmentée et l’impression 3D industrielle, chaque aspect de la chaîne de valeur est optimisé. Cette révolution numérique promet non seulement d’améliorer la productivité et la qualité, mais aussi de permettre une personnalisation de masse à des coûts compétitifs. Comment ces technologies de pointe façonnent-elles concrètement l’avenir de l’industrie ?
Évolution des systèmes cyber-physiques dans l’industrie 4.0
Les systèmes cyber-physiques (CPS) constituent l’épine dorsale de l’industrie 4.0. Ces systèmes intègrent étroitement les capacités de calcul, de communication et de contrôle avec les processus physiques, créant une boucle de rétroaction continue entre le monde virtuel et réel. Dans le contexte industriel, les CPS permettent une surveillance en temps réel, une prise de décision autonome et une optimisation dynamique des processus de production.
L’évolution des CPS a considérablement accéléré le passage vers des usines véritablement intelligentes. Ces systèmes sophistiqués collectent et analysent des volumes massifs de données provenant de capteurs répartis dans toute l’usine, permettant une visibilité sans précédent sur l’ensemble des opérations. Grâce à des algorithmes avancés, les CPS peuvent prédire les pannes d’équipement, ajuster automatiquement les paramètres de production et optimiser l’utilisation des ressources en temps réel.
Un exemple concret de l’impact des CPS est leur capacité à faciliter la production adaptative . Dans une usine équipée de systèmes cyber-physiques avancés, la ligne de production peut s’ajuster automatiquement en fonction de la demande du marché, des niveaux de stock ou même des préférences individuelles des clients. Cette flexibilité permet aux fabricants de répondre rapidement aux changements du marché et de minimiser les gaspillages, tout en maintenant une qualité constante.
Les systèmes cyber-physiques transforment les usines en organismes intelligents, capables d’apprendre et de s’adapter en temps réel aux conditions changeantes du marché et de la production.
Integration de l’internet des objets industriels (IIoT)
L’Internet des Objets Industriels (IIoT) étend le concept de l’IoT grand public au domaine manufacturier, créant un réseau interconnecté de machines, d’outils et de systèmes capables de communiquer et de partager des données en temps réel. Cette connectivité omniprésente est le fondement de l’usine intelligente, permettant une visibilité et un contrôle sans précédent sur l’ensemble du processus de production.
Protocoles de communication M2M avancés
Au cœur de l’IIoT se trouvent des protocoles de communication machine-à-machine (M2M) avancés qui permettent un échange de données fluide et sécurisé entre les différents composants de l’usine. Des protocoles tels que MQTT (Message Queuing Telemetry Transport) et OPC UA (Open Platform Communications Unified Architecture) sont devenus des standards de l’industrie, offrant une interopérabilité robuste entre des équipements de différents fabricants.
Ces protocoles facilitent non seulement la communication entre les machines sur le plancher de l’usine, mais permettent également l’intégration avec des systèmes de niveau supérieur comme les ERP (Enterprise Resource Planning) et les MES (Manufacturing Execution Systems). Cette intégration verticale crée une chaîne de valeur numérique transparente, de la commande client à la livraison du produit fini.
Capteurs intelligents et actionneurs connectés
Les capteurs intelligents et les actionneurs connectés forment le système nerveux de l’usine 4.0. Ces dispositifs, équipés de capacités de traitement et de communication intégrées, peuvent collecter et transmettre des données en temps réel sur pratiquement tous les aspects du processus de production. Des paramètres tels que la température, la pression, la vibration ou la consommation d’énergie sont constamment surveillés, permettant une détection précoce des anomalies et une optimisation continue des processus.
L’utilisation de capteurs intelligents a révolutionné la maintenance industrielle, en permettant le passage d’une approche réactive ou préventive à une stratégie prédictive . En analysant les données historiques et en temps réel des équipements, il est possible de prédire avec précision quand une machine nécessitera une maintenance, réduisant ainsi les temps d’arrêt imprévus et optimisant les coûts de maintenance.
Plateforme IIoT siemens MindSphere
Parmi les plateformes IIoT leaders du marché, Siemens MindSphere se distingue par sa capacité à connecter les équipements physiques au monde numérique de manière transparente. Cette plateforme cloud ouverte permet aux entreprises de collecter et d’analyser de vastes quantités de données provenant de leurs actifs industriels, ouvrant la voie à de nouvelles opportunités d’optimisation et d’innovation.
MindSphere offre une suite d’applications et de services qui permettent aux fabricants de transformer les données brutes en insights actionnables. Par exemple, la plateforme peut être utilisée pour mettre en place des systèmes de maintenance prédictive sophistiqués, optimiser la consommation d’énergie à l’échelle de l’usine, ou encore améliorer la qualité des produits grâce à une analyse approfondie des données de production.
Analyse des données en temps réel avec edge computing
L’edge computing joue un rôle crucial dans l’exploitation efficace des données IIoT. En traitant les données au plus près de leur source, l’edge computing permet une analyse en temps réel, réduit la latence et diminue la charge sur les réseaux et les systèmes centraux. Cette approche est particulièrement précieuse dans les environnements industriels où des décisions rapides peuvent avoir un impact significatif sur la productivité et la sécurité.
Dans une usine 4.0, les dispositifs edge peuvent exécuter des algorithmes complexes directement sur les machines de production, permettant une prise de décision autonome et une optimisation en temps réel. Par exemple, un système de contrôle qualité basé sur l’edge computing peut analyser instantanément les images de chaque produit sortant de la ligne de production, identifiant et rejetant les pièces défectueuses sans aucun délai.
L’intégration de l’IIoT et de l’edge computing crée une synergie puissante, permettant aux usines de réagir en millisecondes aux changements de conditions, assurant une production optimale et une qualité constante.
Intelligence artificielle et apprentissage automatique pour l’optimisation des processus
L’intelligence artificielle (IA) et l’apprentissage automatique (ML) sont au cœur de la transformation numérique de l’industrie 4.0. Ces technologies permettent aux systèmes industriels d’apprendre de leurs expériences, de s’adapter à de nouvelles situations et d’optimiser continuellement leurs performances. Dans le contexte manufacturier, l’IA et le ML sont appliqués à une variété de domaines, de la maintenance prédictive à l’optimisation de la chaîne d’approvisionnement.
Algorithmes prédictifs pour la maintenance préventive
La maintenance prédictive basée sur l’IA représente une avancée majeure par rapport aux approches traditionnelles de maintenance préventive ou réactive. En analysant de vastes ensembles de données historiques et en temps réel provenant des capteurs IIoT, les algorithmes d’apprentissage automatique peuvent prédire avec une grande précision quand un équipement est susceptible de tomber en panne.
Ces prédictions permettent aux entreprises de planifier la maintenance de manière proactive, réduisant ainsi les temps d’arrêt imprévus et prolongeant la durée de vie des équipements. Par exemple, un algorithme ML pourrait analyser les vibrations, la température et d’autres paramètres d’un moteur industriel pour détecter des signes précoces d’usure, permettant une intervention avant qu’une panne ne se produise.
Vision par ordinateur et contrôle qualité automatisé
La vision par ordinateur, alimentée par des réseaux neuronaux profonds, révolutionne le contrôle qualité dans l’industrie manufacturière. Ces systèmes peuvent inspecter des produits à une vitesse et avec une précision bien supérieures à celles des inspecteurs humains, identifiant des défauts subtils que l’œil humain pourrait manquer.
Dans une ligne de production moderne, des caméras haute résolution couplées à des algorithmes de vision par ordinateur peuvent examiner chaque produit en temps réel, assurant un contrôle qualité à 100%. Ces systèmes peuvent non seulement détecter les défauts, mais aussi les classifier et identifier les tendances, permettant une amélioration continue des processus de production.
Systèmes de recommandation pour l’optimisation de la production
Les systèmes de recommandation basés sur l’IA sont de plus en plus utilisés pour optimiser les paramètres de production en temps réel. Ces systèmes analysent une multitude de variables – des conditions environnementales aux caractéristiques des matières premières – pour recommander les paramètres de production optimaux.
Par exemple, dans une usine chimique, un système de recommandation IA pourrait suggérer des ajustements précis des températures, pressions et débits pour maximiser le rendement tout en minimisant la consommation d’énergie. Ces recommandations s’affinent continuellement à mesure que le système apprend des résultats de production, conduisant à une amélioration constante de l’efficacité.
L’intégration de l’IA et du ML dans les processus industriels ne se limite pas à l’optimisation opérationnelle. Ces technologies ouvrent également la voie à de nouveaux modèles commerciaux, tels que la maintenance as a service ou la production as a service , où les fabricants peuvent offrir des garanties de performance basées sur des prédictions IA précises.
Fabrication additive et impression 3D industrielle
La fabrication additive, communément appelée impression 3D, est en train de révolutionner les processus de production industrielle. Cette technologie permet de créer des objets tridimensionnels en déposant des matériaux couche par couche, offrant une flexibilité et une personnalisation sans précédent dans la fabrication.
Dans le contexte de l’industrie 4.0, l’impression 3D industrielle va bien au-delà de la simple production de prototypes. Elle est désormais utilisée pour la fabrication de pièces finales complexes, la production de petites séries et même la création d’outils et de moules personnalisés. Cette technologie permet de réduire considérablement les délais de production et les coûts associés à la fabrication de pièces complexes ou personnalisées.
Un des avantages majeurs de la fabrication additive est sa capacité à produire des géométries complexes impossibles à réaliser avec les méthodes traditionnelles. Cette liberté de conception permet aux ingénieurs de créer des pièces optimisées pour la performance, réduisant le poids tout en augmentant la résistance. Dans l’industrie aérospatiale, par exemple, l’impression 3D est utilisée pour produire des composants d’avion plus légers et plus efficaces, contribuant à réduire la consommation de carburant.
La fabrication additive joue également un rôle crucial dans la personnalisation de masse , permettant aux entreprises de produire des produits sur mesure à des coûts proches de ceux de la production en série. Cette capacité ouvre de nouvelles opportunités dans des secteurs tels que l’industrie médicale, où des implants et prothèses personnalisés peuvent être produits rapidement et à moindre coût.
L’impression 3D industrielle n’est pas seulement une technologie de production, c’est un catalyseur d’innovation qui repousse les limites de ce qui est possible en fabrication.
Réalité augmentée et jumeaux numériques dans la production
La réalité augmentée (RA) et les jumeaux numériques représentent deux technologies transformatrices qui redéfinissent la façon dont les opérations industrielles sont visualisées, simulées et optimisées. Ces technologies créent un pont entre le monde physique et numérique, offrant de nouvelles perspectives sur les processus de production et facilitant la prise de décision basée sur des données en temps réel.
Conception assistée par RA avec microsoft HoloLens
La réalité augmentée, notamment à travers des dispositifs comme Microsoft HoloLens, révolutionne la conception et la planification industrielle. Les ingénieurs peuvent désormais visualiser des modèles 3D de machines ou de produits superposés à l’environnement réel, permettant une évaluation plus précise de l’intégration et de l’ergonomie avant même la production physique.
Par exemple, lors de la conception d’une nouvelle ligne de production, les ingénieurs peuvent utiliser HoloLens pour visualiser l’agencement des machines dans l’espace réel de l’usine. Cette approche permet d’optimiser le flux de travail, d’identifier les problèmes potentiels d’ergonomie et de sécurité, et de réduire considérablement le temps et les coûts associés aux modifications ultérieures.
Simulation de processus avec siemens tecnomatix
Siemens Tecnomatix est une suite logicielle de pointe pour la simulation de processus industriels qui s’intègre parfaitement dans le concept de jumeau numérique. Cette plateforme permet de créer des répliques virtuelles détaillées de lignes de production entières, offrant aux ingénieurs la possibilité de simuler et d’optimiser les processus avant leur mise en œuvre physique.
Avec Tecnomatix, les entreprises peuvent tester différents scénarios
Avec Tecnomatix, les entreprises peuvent tester différents scénarios de production, optimiser l’agencement des équipements et identifier les goulots d’étranglement potentiels avant même que la première machine ne soit installée. Cette approche réduit considérablement les risques et les coûts associés à la mise en place de nouvelles lignes de production ou à la modification de lignes existantes.
Maintenance prédictive basée sur les jumeaux numériques
Les jumeaux numériques jouent un rôle crucial dans la maintenance prédictive moderne. En créant une réplique virtuelle exacte d’un équipement ou d’un système, les entreprises peuvent surveiller en temps réel l’état de leurs actifs et prédire avec précision les besoins de maintenance. Cette approche permet de passer d’une maintenance réactive ou préventive à une maintenance véritablement prédictive, optimisant ainsi les coûts et minimisant les temps d’arrêt.
Par exemple, le jumeau numérique d’une turbine éolienne peut intégrer des données en temps réel sur les vibrations, la température et d’autres paramètres critiques. En analysant ces données et en les comparant à des modèles historiques, le système peut prédire quand une pièce spécifique est susceptible de défaillir, permettant ainsi une intervention proactive avant qu’une panne ne se produise.
Formation des opérateurs en environnement virtuel
La réalité augmentée et les jumeaux numériques transforment également la formation des opérateurs industriels. Les environnements virtuels permettent aux employés de s’entraîner sur des répliques exactes des équipements qu’ils utiliseront, sans les risques ou les coûts associés à la formation sur des machines réelles.
Ces plateformes de formation immersives peuvent simuler diverses situations, y compris des scénarios d’urgence rarement rencontrés dans la réalité. Cette approche améliore non seulement les compétences techniques des opérateurs, mais renforce également leur capacité à réagir efficacement dans des situations critiques.
La combinaison de la réalité augmentée et des jumeaux numériques crée un environnement industriel où la frontière entre le physique et le virtuel s’estompe, ouvrant de nouvelles possibilités pour l’optimisation, la sécurité et l’innovation.
Cybersécurité et protection des données industrielles
Avec la numérisation croissante de l’industrie 4.0, la cybersécurité est devenue un enjeu crucial pour les entreprises manufacturières. La connectivité accrue des systèmes industriels, bien qu’offrant de nombreux avantages, crée également de nouvelles vulnérabilités qui peuvent être exploitées par des acteurs malveillants. La protection des données industrielles et la sécurisation des systèmes de contrôle sont désormais des priorités absolues pour garantir la continuité des opérations et la protection des secrets industriels.
Les menaces cybernétiques dans le secteur industriel peuvent avoir des conséquences particulièrement graves, allant de l’arrêt de la production à des dommages physiques aux équipements, voire à des risques pour la sécurité des travailleurs. Des attaques notoires comme Stuxnet ont démontré la capacité des cyberattaques à causer des dommages réels aux infrastructures industrielles.
Pour faire face à ces défis, les entreprises adoptent des stratégies de cybersécurité multicouches. Cela inclut la mise en place de pare-feu industriels robustes, la segmentation des réseaux pour isoler les systèmes critiques, et l’utilisation de protocoles de communication sécurisés. La formation des employés à la cybersécurité est également cruciale, car les erreurs humaines restent une des principales sources de vulnérabilité.
L’authentification multifactorielle et le contrôle d’accès basé sur les rôles sont devenus des pratiques standard pour sécuriser l’accès aux systèmes industriels critiques. De plus, les entreprises investissent dans des solutions de détection et de réponse aux incidents avancées, capables d’identifier et de neutraliser rapidement les menaces potentielles.
Dans l’ère de l’industrie 4.0, la cybersécurité n’est plus une option mais une nécessité stratégique pour assurer la résilience et la compétitivité des entreprises manufacturières.
En conclusion, le développement technologique façonne profondément l’industrie 4.0, transformant les usines en écosystèmes intelligents, connectés et hautement optimisés. De l’intégration de l’IoT industriel à l’utilisation de l’intelligence artificielle pour l’optimisation des processus, en passant par la réalité augmentée et les jumeaux numériques, ces innovations redéfinissent les paradigmes de production. Cependant, avec ces avancées viennent de nouveaux défis, notamment en matière de cybersécurité, qui nécessitent une vigilance constante et des stratégies adaptées. L’industrie 4.0 n’est pas seulement une évolution technologique, mais une transformation complète de la façon dont nous concevons, produisons et interagissons avec les produits manufacturés.